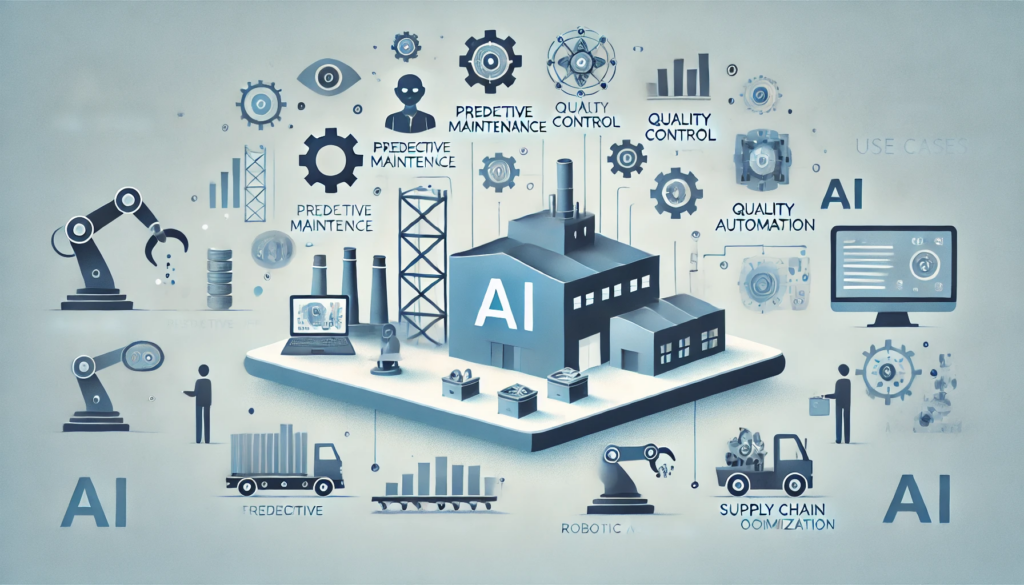
Artificial Intelligence (AI) is rapidly transforming the manufacturing industry, ushering in the fourth industrial revolution—commonly referred to as Industry 4.0. With growing demands for efficiency, precision, and scalability, manufacturers are increasingly turning to AI to optimize operations, reduce costs, and drive innovation. From predictive maintenance and quality control to supply chain optimization and smart automation, AI technologies are reshaping the future of manufacturing.
This blog explores the current trends in AI adoption within the manufacturing sector, key applications, benefits, challenges, and what the future may hold for AI-powered industrial transformation.
Why Manufacturing is Embracing AI
Manufacturing is inherently complex and data-intensive. Operations involve managing supply chains, coordinating machinery, ensuring product quality, minimizing downtime, and maximizing throughput. As such, manufacturers are uniquely positioned to benefit from AI, particularly in the following areas:
- Data-Driven Decision Making: Vast volumes of data from machines, sensors, and systems can be analyzed in real time for actionable insights.
- Automation Potential: Repetitive tasks and workflows are ideal for AI-powered automation.
- Competitive Pressures: Global competition compels manufacturers to innovate and cut costs.
- Labor Shortages: Skilled labor shortages in key areas like maintenance and quality control can be supplemented with intelligent systems.
Key AI Applications in Manufacturing
1. Predictive Maintenance
One of the earliest and most impactful uses of AI in manufacturing is predictive maintenance. AI models analyze sensor data from equipment to predict when machines are likely to fail. This enables proactive maintenance, reducing unplanned downtime and extending asset life.
Trend Insight: Predictive maintenance is now evolving from simple threshold-based alerts to more sophisticated AI models incorporating deep learning and real-time monitoring.
2. Quality Control and Defect Detection
AI-powered computer vision systems are revolutionizing quality assurance. Cameras on assembly lines capture images, and machine learning algorithms identify defects with high accuracy.
Trend Insight: Manufacturers are moving from random sample inspections to 100% in-line inspections using AI, increasing reliability and reducing waste.
3. Supply Chain Optimization
AI helps manufacturers manage complex supply chains by forecasting demand, optimizing inventory levels, identifying bottlenecks, and responding to market fluctuations.
Trend Insight: Integration of AI with IoT (Internet of Things) is enabling real-time supply chain visibility, allowing for dynamic decision-making.
4. Production Scheduling and Process Optimization
AI algorithms optimize production schedules based on factors like order priority, equipment availability, and labor shifts. This ensures higher efficiency and better resource utilization.
Trend Insight: Manufacturers are increasingly adopting reinforcement learning techniques to continuously improve scheduling based on operational feedback.
5. Robotics and Smart Automation
Collaborative robots (cobots) powered by AI are being used alongside human workers to perform complex tasks. AI enables these robots to adapt to changes in the environment and learn from human behavior.
Trend Insight: Smart robots are being trained using simulation environments before being deployed on the factory floor, speeding up implementation.
6. Energy Management
AI analyzes energy consumption patterns to recommend energy-saving strategies, leading to more sustainable operations and reduced costs.
Trend Insight: AI is playing a crucial role in helping manufacturers meet sustainability goals by optimizing energy use and reducing waste.
Sectors Leading AI Adoption in Manufacturing
While AI adoption varies by industry, the following sectors are at the forefront:
- Automotive: Leading the charge in AI adoption with smart factories, autonomous robots, and advanced defect detection.
- Electronics: Using AI for high-precision manufacturing, component tracking, and process control.
- Pharmaceuticals: Employing AI for quality control, formulation optimization, and predictive maintenance in cleanrooms.
- Aerospace: Leveraging AI for part fabrication, inspection, and predictive analytics to maintain safety and precision.
Emerging Trends in AI Adoption
1. AI and Digital Twins
Digital twins—virtual replicas of physical systems—are becoming more prevalent. AI models simulate production lines, machines, or entire factories, enabling predictive insights and scenario planning.
Impact: Engineers can test changes virtually before implementing them, reducing risks and accelerating innovation.
2. Edge AI in Manufacturing
Instead of sending data to the cloud for processing, Edge AI processes data locally on devices near the source. This reduces latency, enhances real-time responsiveness, and lowers bandwidth costs.
Use Case: Edge AI is being used in robotic arms and quality inspection cameras to deliver instant feedback and corrections.
3. AI-Powered Human-Machine Collaboration
AI is enabling smarter interfaces between workers and machines, including voice-controlled systems, AR (Augmented Reality) assistants, and gesture-based controls.
Impact: Enhances worker productivity and safety, especially in complex assembly or maintenance tasks.
4. AI in Additive Manufacturing (3D Printing)
AI is optimizing design parameters, print paths, and material selection in additive manufacturing, making it faster, more cost-effective, and scalable.
Trend: AI is helping automate design validation and detect flaws during the printing process.
Benefits of AI in Manufacturing
The adoption of AI offers numerous tangible benefits:
- Reduced Downtime: Predictive maintenance avoids unexpected failures.
- Improved Product Quality: AI ensures consistent quality and minimizes defects.
- Increased Operational Efficiency: Automated scheduling and workflow optimization maximize output.
- Lower Operational Costs: AI reduces energy consumption, waste, and manual labor dependency.
- Greater Agility: AI enables real-time decision-making and quick adaptation to market changes.
Challenges to AI Adoption
Despite the advantages, manufacturers face several barriers in adopting AI:
1. High Implementation Costs
AI solutions often require significant upfront investment in hardware, software, and infrastructure.
2. Data Integration Issues
Manufacturers use diverse legacy systems that may not easily integrate with modern AI platforms.
3. Lack of Skilled Workforce
There is a shortage of talent with expertise in both manufacturing and AI technologies.
4. Change Management
Cultural resistance to automation and change can slow down AI adoption.
5. Cybersecurity Risks
As factories become more connected, the risk of cyber-attacks increases, especially when AI systems are linked to operational controls.
Strategies for Successful AI Implementation
To effectively adopt AI in manufacturing, organizations should consider the following steps:
- Start Small: Begin with a pilot project that targets a specific pain point and demonstrates ROI.
- Ensure Data Readiness: Clean, structured, and well-labeled data is critical for training accurate AI models.
- Invest in Talent and Training: Upskill current employees and hire AI-savvy professionals.
- Partner with Technology Providers: Collaborate with vendors who offer scalable and customizable AI solutions.
- Prioritize Cybersecurity: Protect AI systems with robust security measures and regular audits.
- Establish KPIs: Set clear metrics to measure the success of AI initiatives, such as reduction in downtime, defect rates, or energy usage.
Future Outlook
The future of AI in manufacturing is incredibly promising. As technologies like 5G, edge computing, and advanced machine learning mature, we can expect:
- Hyper-Automated Smart Factories: Where machines learn and adapt in real time with minimal human intervention.
- Mass Customization: AI will enable manufacturers to produce highly customized products at scale.
- Autonomous Supply Chains: AI will handle forecasting, procurement, and logistics dynamically with little human oversight.
- Sustainable Manufacturing: AI will drive eco-friendly operations, energy optimization, and waste reduction.
Global spending on AI in manufacturing is expected to grow exponentially in the coming years, with both large enterprises and SMEs investing in intelligent systems to stay competitive.
Conclusion
AI is not just a tool for automation—it is a strategic enabler for transformation in the manufacturing sector. The rapid adoption of AI is empowering manufacturers to improve quality, reduce costs, and become more agile in an increasingly dynamic market environment.
As AI technologies continue to evolve, manufacturers must not only invest in systems but also in people, data strategies, and cultural readiness. By doing so, they can unlock the full potential of AI and usher in a new era of smart manufacturing.
Whether you’re a factory manager, supply chain director, or industrial innovator, embracing AI is no longer optional—it’s essential for future growth and sustainability.